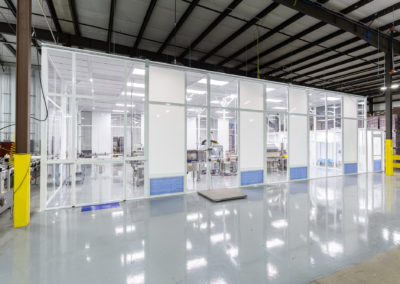
RigidWall Cleanroom Features
We’ve already published blogs about SoftWall and HardWall cleanroom features (check them out if you haven’t yet!). So, this article will finish up the series by diving into RigidWall cleanrooms. We’ll discuss what they are, what unique features they offer, and what benefits they could bring to your facility.
What Are RigidWall Cleanrooms?
RigidWall cleanrooms are constructed with aluminum extrusions, and are somewhat of a mixture between HardWall and SoftWall cleanrooms. They are durable and flexible, much like the HardWall, and more robust than the SoftWall. They have the same once-through configuration and design that SoftWall cleanrooms offer.
You might recognize a RigidWall cleanroom by paying attention to one specific aspect of them: aesthetics. RigidWall cleanrooms are generally built with transparent panel inserts that provide full visibility into the room, from floor to ceiling.
Because of this trait, RigidWall cleanrooms are a common choice for applications that require the transparency aspect. This could include processes that require outside monitoring and safety or use as a show piece for new and potential customers.
RigidWall Cleanroom Features
Just like the other types of cleanrooms, RigidWall cleanrooms can be customized to meet specific customer needs. However, every RigidWall cleanroom does have a certain list of basic features. We’ll walk through them in the three sections below.
RigidWall Cleanroom Materials
The most prominent material in RigidWall cleanrooms is their transparent wall panel inserts. We outline those, as well as some of their other structural materials below:
- Wall Panels – RigidWall panels are prefabricated utilizing high-strength aluminum extrusions that are finished with white powder baked enamel with ¼” inserts. They can be composed of ¼” acrylic, static dissipative PVC, or polycarbonate. The inserts can be either clear or opaque.
- Ceiling System – The RigidWall structural ceiling system follows a T-grid layout, and is composed of 2” extruded aluminum framework. It holds necessary equipment like fan filters, ceiling tiles, and lighting.
- Entrances – RigidWall cleanrooms are compatible with the same types of entrances as HardWall cleanrooms: swing doors, overhead doors, automatic or manual sliding doors, and more.
RigidWall Cleanroom Sizes
No matter the size of your cleanroom, a RigidWall solution can meet the requirement. Standard rooms are available in 2’x4’ increments and can free span up to 30’. Their standard prefabricated panels are available in the same size as HardWall panels — so 4’ wide and 8’ tall nominally.
RigidWall Cleanroom Standards
Due to their solid, durable wall systems, RigidWall cleanrooms are capable of meeting ISO classification between ISO Class 5-8.
Benefits of RigidWall Cleanrooms
RigidWall cleanrooms aren’t the most common type of cleanroom we build at Angstrom Technology, but they’re highly rewarding solutions for the right applications. Below are some of the unique benefits they offer.
Sleek Appearance
RigidWall cleanrooms’ transparent appearance offers a sleek, transparent style that other types of cleanrooms don’t. For applications that require full visibility into the cleanroom, this is a great option.
Good Contamination Control
RigidWall cleanrooms offer control over contamination, static, pressure, and airborne particulates. As mentioned above, their level of control can meet ISO Class 5-8 requirements.
However, it should be noted that RigidWall cleanroom panels don’t have the insulation properties needed for regulating temperature and humidity. If your application requires stringent temperature and/or humidity control, a HardWall cleanroom is a better option. HardWall cleanrooms offer great control over contamination, particulate matter, and temperature and humidity.
Great Reconfigurability
Since RigidWall cleanrooms are constructed with prefabricated, modular wall panels, they can be easily reconfigured to change with you. As your facility evolves and grows, your RigidWall cleanroom can seamlessly evolve and grow too. It also improves the ability to include new types of equipment or technology within your cleanroom if need be. No matter what your needs are or may be in the future, a RigidWall cleanroom is a long-lasting solution.
Extreme Durability
High-strength 6063-T6 aluminum extrusions, a robust 2” ceiling system, and reliable structural framework make RigidWall cleanrooms highly durable. Their coat of white, powder-baked enamel prevents corroding and contamination. Also, because the system requires no drilling and tapping, it’s quite clean and easy to install.
Simple Cleaning & Maintenance
RigidWall cleanrooms have non-porous surfaces and specific powder baked enamel finishes that make routine cleaning easy without rust or corrosion. You can wipe down all of these surfaces with cleanroom-approved cleaning products quickly and easily. This is a great advantage, especially for cleanroom applications that require very frequent cleanings to ensure their safety.
Interested in installing a RigidWall cleanroom in your facility, or have questions about which type of cleanroom is right for your application? Let us know! Our cleanroom design and installation team can deliver a solution that meets your unique specifications. Give us a call at (888) 768-6900 or contact us online today.